Introduction: In practical applications, it is recommended to use different gaps to choose different thicknesses of thermal silica film.
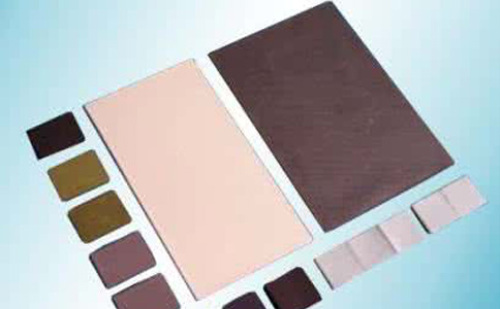
The thermal silica film is designed to fill the gap between the heat generating element and the heat sink. The surface of metal components cannot be absolutely smooth and flat. Some surfaces with a flat surface that look like a human eye are under the microscope. Gutters and grooves are formed when the two metal surfaces that seem to be flat but actually meander together. The metal is hard and difficult to compress effectively, so there is a large gap in the middle, and air is a poor conductor of heat. At this time, the thermal conductivity will be greatly reduced, and the temperature of the components cannot be effectively reduced. Therefore, a material is needed to fill the gap. Reduce the thermal resistance, improve the heat transfer efficiency, and ensure the working stability of the functional device, so the interface thermal material came into being.
Early thermal conductive materials were most commonly used for thermal greases. They were widely used in computer mainframes and other electronic products. However, thermal greases are inconvenient to operate, and improper smearing can easily contaminate components. With a long time, they will fail due to volatilization of silicone oil. With the advent of thermal silica films, applications in some areas have also replaced thermal greases. Thermally conductive silicone sheet is sheet-like, soft and elastic, high compressibility, self-contained micro-viscous, easy to install, conducive to maintenance, stable thermal conductivity, no silicone oil volatilization and failure, excellent insulation, a wide range of thickness (0.3 ~ 15mm ) These characteristics are not available in silicone grease.
The application of thermal silica film is not only limited to the filling between two relatively flat surfaces, many thermal silica films can also be selected for the filling of interfaces such as pins with large gaps.
Theoretically, it can be known that the thermal resistance is proportional to the distance of heat transfer. The greater the thermal resistance, the more unfavorable the cooling of the functional device. Therefore, the thickness should be selected when selecting the thermal silica film, if it is on two flat surfaces. When filling, the thickness should be 0.3 or 0.5mm. On the one hand, the thermal conductivity is high, and on the other hand, the cost is reduced. When the gap is large, the assumption is 2mm. At this time, the thickness of 2.5mm or 3mm thermal silica film should be selected. If 2mm is selected, the air cannot be effectively discharged, and the thermal conductivity cannot be normalized. The silica gel sheet has a compressibility, and the greater the pressure on the thermal silica sheet, the better the thermal conductivity. Therefore, considering comprehensive thermal conductivity and cost considerations, choosing 2.5 to 3.0 is optimal.
In practical applications, different thicknesses of thermally conductive silica gel sheets can be selected in combination with different gaps. The thermal conductivity layer is based on the power consumption of the heating device to make a choice, generally low power consumption, such as led downlights, led spotlights, etc. Select LC1 1.2w/mk thermal conductivity of thermal conductivity of silica film can meet its thermal conductivity , Higher power consumption, such as LED lights, led light miner's lamp and other choices of the 1.7 ~ 2.0w/mk thermal conductivity of the LC170/LC200 can meet its thermal conductivity. Then high power consumption, you can choose high thermal conductivity, such as 3.0 ~ 8.0w/mk thermal conductivity of high thermal conductivity silicone film.
At present, many manufacturers can provide samples for free, and can take samples and tests before making decisions. This is the most direct and accurate method.
Disposable electronic cigarettes
vape e cigarette device,vape disposable puff bar,vape disposable,smoke vape pen,smoke pen vape
Shenzhen Aierbaita Technology Co., Ltd. , https://www.aierbaitavape.com